CONVEYING SYSTEMS
- what ıs the pneumatıc conveyıng system?
-
DOSERAY dilute phase pneumatic conveying
systems range from single-point "up-and-in" installations to
cross-plant systems with multiple pick-up and discharge points and
automated controls, satisfying an exceptionally wide range of bulk
conveying applications. All are custom-engineered and fully
integrated with other DOSERAY equipment and systems, and your new or
exiSting process.
DOSERAY dilute phase pneumatic conveying systems move bulk materials that are suspended in an air stream that is introduced by a positive pressure blower upstream of material intake points, or by a vacuum pump that removes air from the system downstream of material discharge points. Material is separated from the conveying air at the use point, then discharged on a batch basis via butterfly or slide gate valves, or continuously via rotary airlock valves.
Total evacuation
DOSERAY systems fully evacuate the vessel being discharged and the conveyor line itself, minimizing cross-contamination of multi-ingredient systems. Complete transfer of material also ensures that individual and consolidated batch ingredients reach their deStinations accurately by weight, maximizing quality while minimizing waste. - DOSERAY dılute phase conveyıng
-
These systems utilize a positive displacement blower with single or multiple downstream material entry points, each of which meters product into conveying lines by means of a rotary airlock valve that maintains the pressure differential between the ambient atmosphere and that of the conveying line. Material and air blown through the line exit at single or multiple use points where they are separated by means of a filter receiver or cyclone separator, or fed directly into process vessels that are vented to downstream dust collection devices.
Pressure systems offer higher efficiency than vacuum systems, can convey over longer distances, and can blow directly into process and storage vessels without the use of a rotary airlock valve
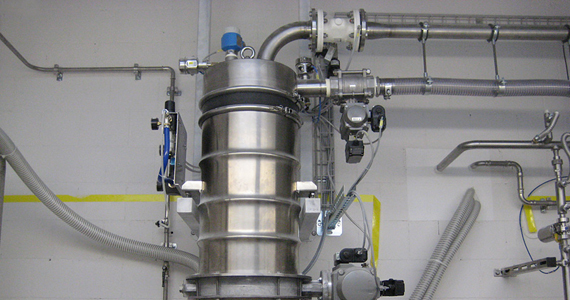
Vacuum dilute phase pneumatic conveying systems are generally
employed for transporting material from multiple sources such as
storage vessels, process equipment, trucks and railcars, to
individual or multiple deStinations. Unlike positive pressure
systems, vacuum systems allow easy pick-up of materials from open
containers using wands, and do not impart heat to the material.
Since vacuum systems offer superior leak containment, they are
often specified on the basis of cleanliness, particularly when
handling hazardous materials. Negative pressure is
created by a positive displacement vacuum pump located at the
downstream end of the system. Material typically enters the system
via upstream rotary airlock valves, hand-held pick-up wands, and
non-flow-through/flood-feed pick-up adapters, and exits the system
through filter receivers or cyclone separators that separate the
material from the conveying air directly above process equipment,
surge hoppers, storage vessels or other discharge points.
In
addition, vacuum conveying is suited to direct feeding of
blenders, reactors and other enclosed process vessels that are put
under vacuum by a line terminating at a downstream bag house or
other dust collection device, eliminating the need for individual
filter receivers or cyclone separators above each discharge point.
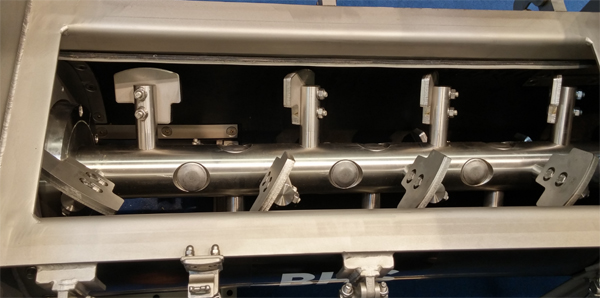
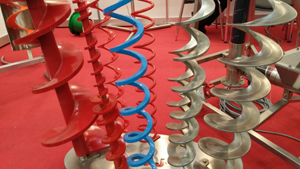
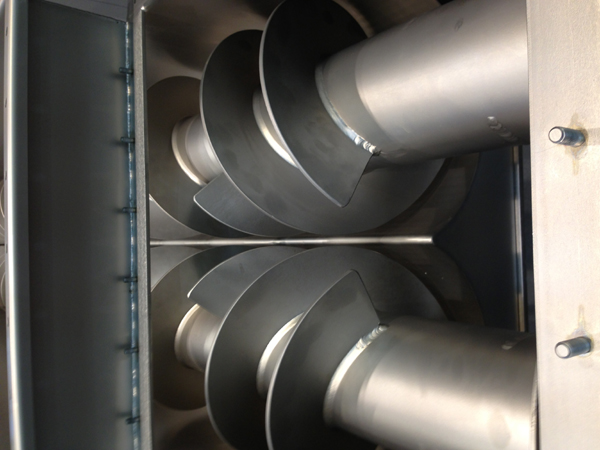
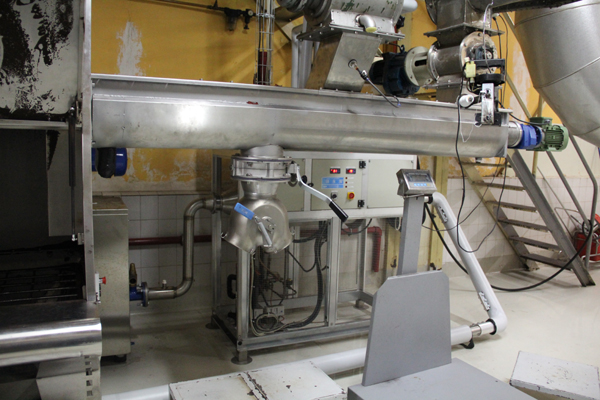
-Inlet is always control fed
-Trough loading of 15, 30, and 45%
-Volumetric conveying device
The inlet is usually flooded with material (100% loaded)
Volumetric metering device Ribbon Flight Conveyors consist of sectional flights, butt-welded to form a continuous helix. The flights are secured to the center pipe by supporting legs. Ribbon flight conveyors are used to convey tacky, gummy, or viscous substances, or in applications where the material tends to adhere to the flighting and pipe.
Paddle Screw Conveyors are used in applications where material needs to be mixed before reaching its deStination. Adjustable paddles provide complete mixing action and controlled material flow. Conveying action can be controlled by adjuSting the angle of the paddles.
Screw Feeders move a wide variety of material from bins or hoppers at a constant and controlled rate of flow. One or more tapered or variable pitch screws convey the material at the required rate. Screw feeders are available in a variety of types to suit specific materials and applications.
-Inlet is always flood loaded
-100% trough loading at inlet
-Volumetric metering device
Labels: pneumatic conveying, mechanic conveying, screw conveying system,vacuum conveying, dosing systems,pneumatic conveying